ピンホールの問題とは?耐ピンホール性の重要性
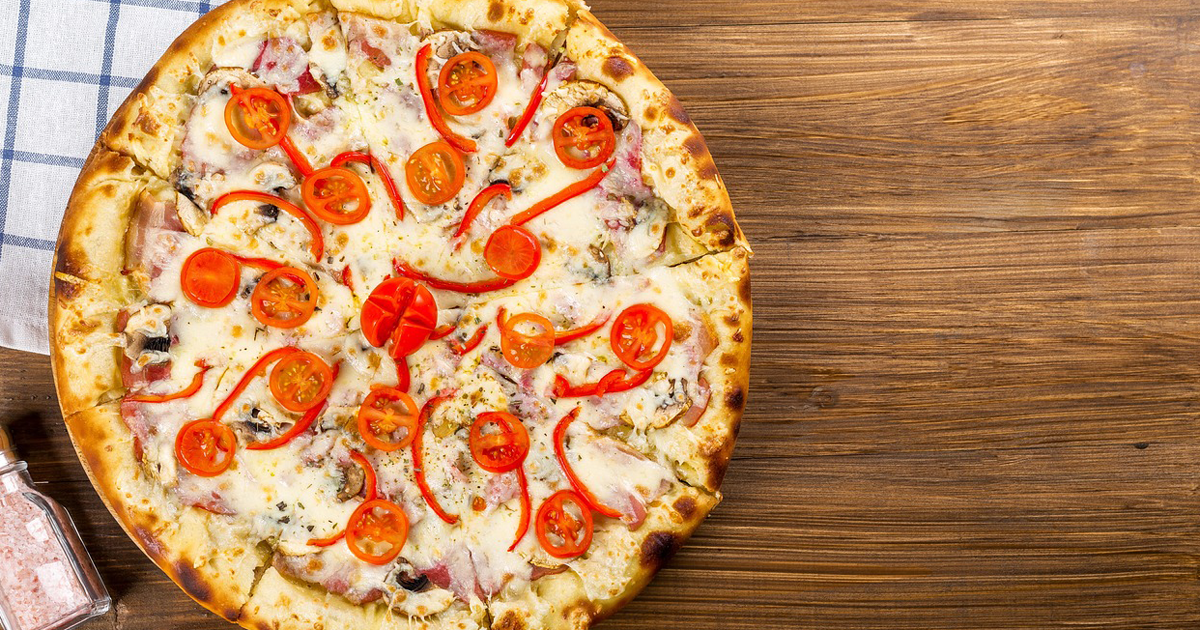
耐ピンホール性の向上における素材選定のポイント
耐ピンホール性の向上は、製品の品質維持と安全性確保に直結する重要な課題です。
素材選定はその鍵となります。
以下に、耐ピンホール性を向上させるための素材選定のポイントを紹介します。
1. バリア性能の高い素材: 耐ピンホール性を向上させるには、外部からの影響を最小限に抑えるバリア性能の高い素材を選ぶことが重要です。
酸素や湿気の侵入を防ぐ効果がある素材を選びましょう。
2. 均一な素材品質: 素材の品質は耐ピンホール性に大きな影響を与えます。
均一な品質を持つ素材を選ぶことで、穴や隙間が発生しにくくなります。
3. 剛性と柔軟性のバランス: 素材の剛性と柔軟性のバランスを考慮することで、耐ピンホール性を向上させつつ、製品の取り扱いや加工のしやすさを保ちます。
4. 耐久性: 耐ピンホール性フィルムは長期間にわたって安定した性能を発揮する必要があります。
耐久性が高い素材を選ぶことで、製品の寿命を延ばすことができます。
5. 環境への影響: 環境に配慮した素材を選ぶことで、製品の耐ピンホール性向上と同時に環境への影響を最小限に抑えることができます。
素材選定は耐ピンホール性の向上において重要なステップです。
バリア性能や均一な品質、剛性と柔軟性のバランスを考慮しつつ、製品の品質と安全性を確保する素材を選びましょう。
フィルム製造工程でのピンホール対策とは
フィルムの製造工程において、ピンホールの発生を最小限に抑えるためには慎重な対策が求められます。
以下に、フィルム製造工程でのピンホール対策について説明します。
まず、原材料の選定。
耐ピンホール性に優れた高品質な原材料の使用が重要です。
均一な品質を持つ原材料を選び、微細な穴や隙間の発生を防ぎます。
次に、製造プロセスの最適化。
製造プロセスを最適化することで、均一な厚みや質感を実現します。
不均一な部分が生じることでピンホールのリスクが増加するため、工程のコントロールが重要です。
また、製造工程をクリーンルームで行うことで、微粒子や異物の侵入を防ぎ、ピンホールの発生を抑制します。
さらに、製品のテストと検査を通じて、ピンホールの有無を確認します。
早い段階で問題を検出し、修正することで最終製品の品質を向上させます。
加えて、従業員に対して適切なトレーニングを提供することも重要です。
ピンホールの原因や発生メカニズムを理解してもらうことで、従業員の意識向上が問題の予防に繋がります。
フィルム製造工程でのピンホール対策は、品質維持と安全性確保のために欠かせない要素です。
原材料の選定から製造プロセスの最適化、検査体制の強化まで、綿密な対策が品質向上に寄与します。